Proventech has been associated with USV for 3 years now supporting the Serialisation -US DSCSA, EUFMD, DS & now QR code on blisters.
We are happy to share our experience as a satisfied customer of ProvenTech, a company that has exceeded our expectations and has truly delivered their solutions to meet our business requirements.
The team at ProvenTech demonstrated exceptional expertise, professionalism and dedication all the time. From the initial consultation to the implementation of their solutions, they exhibited a deep understanding of our business goals and objectives. Their ability to translate our complex requirements into efficient solutions through their expertise.
One of the most remarkable aspects of working with ProvenTech was their commitment to providing top-notch customer service. Anytime we had a question or concern, their support team was quick to respond and resolve any issues promptly.
We are fully satisfied with their support and look forward to a long-lasting association.
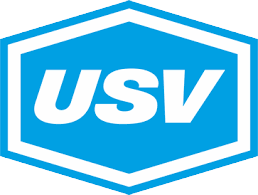
Mangesh Gupte,
Sr. GM-Projects
USV Private Limited

I am happy to share my testimonial for our new service provider ProvenTech.
From the moment we partnered with them, we experienced a level of professionalism and dedication that surpassed all our expectations.
Their team is comprised of true experts in their field, and it's evident that they understand the business requirements and map the tailormade solutions to address day to day business user pain points. Whenever we had questions or required assistance, they were always just a phone call or email away, ready to provide prompt support. What impressed me the most was their commitment. Not only they delivered exceptional results, but they also did within the agreed-upon timeframe and budget.
I highly recommend ProvenTech to anyone seeking professional, reliable, and results-driven solutions. They have been an invaluable service provider to any organization, and I look forward to continuing this good relationship for future endeavours.
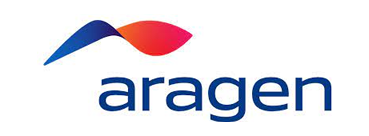
Anil Gopal Yellapragada,
Associate Director

When we have a urge to check all our chromatographic data for some of the critical aspects, Proventech team has given us a tool to verify the data and make us to complete the task with their support in very tiniest timelines. I really appreciate the team for their support though out the work , we are planning to get proventech support for all critical and time taking works. Once again thanks to the proventech team.
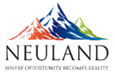
Kishore
Head -QC
Neuland Laboratories Ltd Unit-1

Sharing my experience with Proven Tech (PT) during SAP WMS implementation. When our management decided to implement WMS for 3 vaccine plants in span of 3 months, we were looking for reliable, efficient technology partner, which we find in PT. Since beginning, PT team displayed a deep understanding of our business objectives & processes. Their expertise help use complete the project within timeline as per our business requirements. Recently visited auditors appreciated WMS system, proper documentation and its effectiveness. Overall support from PT were highly appreciable & finally our team is extremely satisfied after WMS implementation.
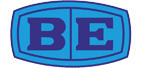
Padmakar Jadhav
G.M. Warehouse.
Biological e Limited
